A good hull features quality construction and durable materials.
Design Considerations
Obviously there are many considerations in considering the design of a hull that properly fall into the domain of a marine architect. Here are some factors that were considered for Sharina. You may have a different list for your project.
- Hull material
- Double hull
- Swim platform
- Bulkheads
- Hull openings
- Keel coolers
Hull Material
The primary materials for hulls are fibreglass, steel or aluminium, wood or ferro-cement. Wood is beautiful but high maintenance, and difficult to repair. Use wood only if you are a confirmed traditionalist. Ferro-cement has a long successful wartime history pre-dating fibreglass [1, 2]. It uses welded or woven wire mesh, or expanded metal lath covered with a sand and cement plaster. It is suited to amateur construction; and has very low resale value.
More exotic materials are being used in super yachts. The Juan K Super Maxi, a 115-ft monohull sail boat, is built from carbon-fibre [3]. In this example, a carbon-fibre hull was 66% lighter than the equivalent aluminium hull. Of course, hull weight is not as critical in a displacement hull.
For a small trawler, fibreglass and steel are your materials of choice. Don’t consider anything else, unless you want to go to sea in a cast-iron bathtub.
In general fibreglass must be three times the thickness of steel for the same tensile and compressive strength but has a 40% lesser weight. Thus fibreglass is better suited than steel to a semi-displacement trawler or a smaller displacement trawler where steel might be too heavy.
Fibreglass
Fibreglass, also called fibre-reinforced plastic (FRP), fibreglass-reinforced polyester, glass-reinforced plastic (GRP) or resinglass, has become the material of choice for production boats because of the lower labour cost. It is less expensive than steel and costs less to maintain. It is suited to limited series production using a mould; whereas steel is more labour-intensive and better suited to one-off construction.
Fibreglass, unlike steel, is not subject to corrosion, or galvanic action. It has a smooth, high-quality finish. Colour can be added to the gel coat, eliminating the need for painting. Small holes can be patched readily using supplies found in marine and automotive centres. Glass grades are type A, E or S but only E-glass (electrical glass) should be used in a boat. In terms of materials and modern technology Sweden, France, UK, and USA have the most to offer.
Fibreglass is more difficult than steel to make a hull leak-proof because hulls and decks are separate components that must be joined, bolted and bonded.
In general, fibreglass is not as strong as steel; although multilayer NIDA [3-1] sandwiches are very strong indeed. It is more easily damaged. It abrades easily, and cannot withstand pounding when grounded. The gel coat can blister, which may or may not be serious, and powder from oxidization and ultraviolet light. When fibreglass is penetrated, water can enter its structure through osmosis, making large sections of hull spongy inside.
Fibreglass by its polyester nature will absorb some water. The use of either vinylester or isopthalic resin below the waterline will increase resistance to blistering [4]. When sections are cut from the hull for portlights and hatches, ask the builder to test them in boiling water for 100 hours to see if they blister. If they don’t, the construction quality is excellent.
Blistering is caused by water-soluble material (WSM) trapped in resin or matt layers next to the gel coat [5]. The WSM ‘attracts’ water, which penetrates the hull through the process of osmosis. Since the WSM has now expanded, the resulting pressure forms a blister. The solution in the blister becomes acidic from chemical reactions between various materials and the water.
Fibreglass construction requires special techniques and skills. There are several techniques. Basic boat building requires a plug or a mould. Fibreglass is laid up by hand using cloth, sprayed using a chopper gun, or vacuum-bagged. It can be built up as a single skin or a foam-core sandwich; and reinforced with aramid fibre or carbon-fibre.
Fibreglass comes in chopped strand mat (CSM), continuous roving (CR) and woven roving (WR). Strand is not structural, so it is best avoided. Experience has shown that alternate layers of CSM and WR are best with extra CSM near the outside. Glass cloth or tape is also available for small repairs.
There are two types of resin: laminating and the previously mentioned gelcoat. “Marine General Purpose” Isophthalic or Neopentyl Glycol polyester resin is used commonly.
To make a mould, you start with a plug in the exact shape of the hull or hull component. The plug is disposable, and can be made from a variety of materials. The exterior of the plug is highly finished.
Next, a fibreglass mould is built up on the plug, using alternate layers of cloth and matt, a felt-like material. Each layer is impregnated with a synthetic polymer resin that cures and hardens. The exterior of the mould is reinforced, and the plug is removed and discarded. The best range for working temperatures in the mould shop are 18-21 C with humidity less than 80%. Direct sunlight should be avoided.
Finally, the inside of the mould is coated with a wax-like release agent, and a fibreglass hull or other component is built up inside, starting with the coloured gel coat, a layer of mat and then woven roving. Putting mat, a sort of filler, next to the gel coat prevents print-through of the roving. Anecdotally, putting mat next to the gel coat increases the propensity for blistering. After the piece is finished and cured, it is removed from the mould for finishing. The mould is then ready for re-use. Gel coats should be >30 mm and incorporate protection from ultraviolet (UV) light, which damages plastics.
Moulds are typically used for limited production. For series production, construction is done using just a plug. With a plug, fibreglass is laid up over the outside of the plug, with a roving layer last, and then hand finished with a gel coat. Today, plugs can be cut using multi-axis robotic milling machines driven by CAD cutting files.
Hand lay-up is not common today, for reasons of efficiency and environment. Special guns that spray resin and chopped glass fibres into the mould have replaced hand lay-up. A more recent technique, vacuum infusion, uses a vacuum bag over the mould to ensure consistent quality [6, 7].
Fibreglass components are made with either a single-skin or a sandwich construction. Single-skin construction uses alternate layers of continuous and woven roving that are saturated with resin and allowed to cure. Typical glass-to-resin ratios are 30:70. Unidirectional and bi-axial reinforcing materials can increase strength while eliminating stress deformation, reducing weight and increasing the glass-to-resin ratio to 50:50, which is better.
Sandwich construction was introduced to reduce material cost. It uses a foam-core material, plywood or balsa wood between two layers of fibreglass. Wood of any kind is not recommended because it readily absorbs water, which will delaminate the sandwich.
Although introduced for cost reasons, a sandwich is stiffer than a single skin, and lighter for the same stiffness. Interestingly, the stiffness is not imparted by the foam-core but by the equal separation of the two skins, and the effect this has on bending forces. Another advantage of a foam sandwich is no extra insulation is required. Usually the final paint is applied in the gel coat.
A sandwich is not as durable as solid 'plastic', partly because more skill is required to ensure the skins bond solidly to the core without voids. Incomplete bonding and voids cause delaminating and failure of the component. These risks can be overcome with vacuum infusion. Bi-axial fibreglass material is recommended with sandwich construction. Some experts advise against any kind of core below the waterline.
Early foam-cores were open cell, which out-gassed and was vulnerable to water absorption. Newer foam cores, such as Airex® [8], Core-Cell® [7], Divinycell® [9] and NIDA [3-1] have closed cells. Note that some like Airex® are susceptible to heat and not suited for use in decks or engine rooms.
Several types of foam core can be used in a sandwich:
- Cross-linked Poly Vinyl Chloride (CL PVC) is typically used in decks, superstructures, hull bottoms and sides, bulkheads, and transoms.
- Styrene Acrylo Nitrile (SAN) is used in areas where high impact is prevalent, such as hull bottoms and sides, e.g., Core-Cell.
- Non-cross-linked or "linear" PVC (L PVC) e.g., Airex® R63, is used in the same areas as SAN.
- Polyurethane (PUR) and polyisocyanurate (PIR) foam are used in acoustical and insulation panels, structural insulation panels (SIP) and parts like stringers [11]. These foams are water resistant, meaning they will absorb some water, around 5%, and encourage mildew.
A honeycombed core such as over-expanded Nomex can be used in dinghies to reduce weight. Honeycomb is not suited to a displacement hull.
Where cost is not a consideration, aramid and carbon fibres can be used to reinforce fibreglass. Aramid [12] is a family of manufactured nylon fibres, including Kevlar®, Nomex® and Twaron, based on long-chain synthetic polyamides. Kevlar® has been used in some small-equipment applications like paddles and in high-speed boat hulls for the US Navy SEALS [13, 37]. In trawlers, the Krogen 58 has Kevlar-reinforced bottoms in the stem and stern areas.
A similar technology is carbon-fibre composites. These are generally too expensive (and too light) for displacement boat hulls but are found widely today in aircraft and automotive parts like wing assemblies, monocoques and body panels where strength and light weight are important [14], or in super yachts like the aforementioned Juan K Super Maxi. The Maxi is a high-speed sail boat, not a displacement boat, so light weight is important.
Steel
Steel hulls are made of plates of Lloyd’s approved marine quality steel. The steel is pre-primed at the steel mill. Plates are precision laser cut, using computerized design instructions called cutting files. Cutting files minimize wasted steel, and ensure a good fit. Deck plating is typically from 5/32-in to 1/4 in (4-6 mm), and hull plating is from 1/4-in to 5/16-in (6-8 mm) in thickness.
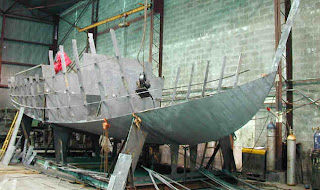
Fig 4-1 – Bruce Roberts Trawler 43 assembled from pre-cut steel plates
– Photo with permission © Bruce Roberts Yachts
– Photo with permission © Bruce Roberts Yachts
Typically the hull is assembled ground up, by raising web frames and longitudinal stiffeners, and then attaching the hull plates, followed by deck plates and superstructure [15]. A few builders are using transverse instead of longitudinal stringers.
Steel construction requires some heavy equipment; and experienced welders to get a fair finish to the hull. Joints are double welded below the waterline. Above, they can be single welded but it is better to weld them inside and out. After welding, joints are ground smooth and filled in where necessary. A team of three welders might take about 1000 hours to assemble a complete 60-ft hull.
A critical join is between the deckhouse and deck. Although the deckhouse could be simply welded to the deck, it is better to have structural pillars extending up from inside the hull. This can be accomplished by having strong mullions. Extreme waves have been known to tear off deckhouses.
Similarly, the bow, keel and bilge keels should be reinforced in case of an accidental grounding.
If you have a larger budget, you could have a steel hull and aluminium superstructure. This reduces weight above decks and keeps the centre of gravity lower. Galvanic corrosion between the dissimilar metals is avoided by using an explosion-bonded bimetallic strip to join the steel and aluminium. These strips were first developed for the US Navy.
The strips are composites of aluminium and steel, bonded together at the molecular level by an explosive force. The aluminium deckhouse is welded to the aluminium strip, while the steel hull is welded to the steel strip.
Steel will give you a homogeneous leak-free hull. It is more difficult than fibreglass to get a fair finish. To prevent corrosion, it must be primed and painted. It must be protected from galvanic action. It is very strong and not damaged easily. It can withstand some pounding when grounded. It will dent before it allows penetration. Any welder anywhere in the world can put a patch on easily.
For Sharina, I chose steel for extreme ruggedness, and ease of construction and repair.
Double Hull
A double hull [35] or double planking is found on the most expensive designs like Cape Horn [16]. A double hull offers additional protection against hull penetration, e.g., by a log or shipping container. About 2,000 containers a year are lost overboard. Many of the smaller ones float for a long time. Containers 40-ft and under have weight limitations for the contents that are low enough to give the containers buoyancy if they are watertight. If they have only small holes and take on water slowly, they can take several months to sink [17]. Containers over 40-ft have no reserve buoyancy and probably sink right away.
A double hull has significant impact on displacement, centre of gravity and, of course, cost. Aluminium superstructures are often used to redress the increased weight. A double bottom only offers no protection from hull penetration by floating objects but does offer some protection from grounding.
Sharina may have a double bottom but not a double hull.
Swim Platform
Let’s face it, swim platforms and staircases on the transom are ugly. Even a ladder with handrails looks better than a staircase. A forward sweeping Euro style transom has the best cool factor. But people do like to swim. And you can’t ask your grandmother to haul herself up a ladder. Also, a swim platform qualifies as an emergency boarding device, which you have to have anyway, and is handy for getting in and out of a dinghy.
A swim platform should have a railing, a low attachment point for a sea anchor, and cleats for a dinghy. It can also be used to mount a stern thruster. Consider filling the swim platform with polyurethane foam. Sharina will have a swim platform. With a staircase. Ugh!

Bulkheads
Watertight Bulkheads
Depending on length, your trawler should have at least four watertight bulkheads, with watertight doors. This is the lesson learned from Titanic. Titanic’s bulkheads stopped short of the deck. When one compartment filled with water, it slopped over into the next. This was fixed in Britannica’s design, but all the doors and port lights were open when she struck the mine. Ever since Titanic, all ships have had watertight bulkheads, most with manual and automatic means of closure on any openings.
The four bulkheads are arranged as follows. There should be an aft bulkhead, at a distance from the stern of 5-8% of the boat length, a collision bulkhead (doubling as a chain locker) in the forepeak, and two other bulkheads in between. The space in the stern can be filled with polyurethane foam. Ideally, none of these bulkheads should have doors in them. They should be entered through deck-level hatches. But from a practical standpoint, doors are unavoidable. Any doors in bulkheads should be watertight. The engine-room door should have a fire-proof view port, so you can peek before charging in.
Make sure bulkheads cannot be breached by back-pressure through the plumbing system.
Acoustical Isolation
Acoustical isolation is extremely important in a live-aboard boat to keep noise within a comfortable range. We experience sound in terms of a frequency range measured in Hertz (Hz) and air pressure measured in decibels (dB). The ear has a very wide non-linear response to the intensity of sound, so each 10 dB increase is ten times louder. Thus a 20 dB increase is 100 times more intense. Duration is also important. Constant noise over 85 dB will damage hearing.
For reference, the ambient noise level in most homes is 30-35 dB. Car interiors are around 40 dB. A normal conversation is around 60 dB. A diesel engine room is around 125 dB. A jet plane taking off is around 140 dB. For bedrooms, the World Health Organization recommends 30 dB with no single noise event exceeding 45 dB.
A good strategy is to eliminate sound at its source, especially in the engine room. This reduces the cost of acoustical insulation elsewhere. Noise attenuation of 100 dB is feasible. Some areas for consideration are:
- Engine and exhaust-system mounts to decouple engine noise from structural members
- Engine enclosures for generators with heat-resistant sound-dampening materials
- Exhaust mufflers
- Air intake baffles
- Flanking noise via holes in bulkheads and water, plumbing and HVAC distribution systems
- Floor, ceiling and walls of the engine room
- Bulkheads and doors in living spaces
- Isolating all wall panels from structural boat walls
Complicating matters a bit, every engine and engine room is a unique case. However, noise radiation from the crank case and oil sump is typically 500 to 1,000 Hz. Engine block vibrations run below 1,250 Hz while gear noises run above 2,000 Hz.
The human ear responds to sounds in the range of 20 Hz to 20 kHz but is most sensitive in the 1,000-5,000 Hz band with a peak around 4,000 Hz. The auditory canal alone has a closed-tube resonance of 2,000-5,000 Hz.
For a production boat it’s feasible to do a spectrum analysis and design suitable sound attenuation and test it. For a bespoke boat this is unlikely to be feasible. Thus a good cost-effective approach is to focus on reducing sound transmission in a target range such as 1,000-2,500 Hz (wavelengths of 13.5 to 5.4-in or 34.3 to 13.72 cm).
Acoustical isolation works by converting sound waves into heat that is then dissipated. Some methods of isolation are:
- Reflecting sound waves
- Dampening sound waves
- Converting sound waves to heat energy
- Decoupling surfaces
Dampening sound is achieved by absorbing it in insulation. The depth of insulation should be calculated to absorb the desired wavelengths (e.g., 6-14 in).
Sound waves can be converted to heat energy by adding mass to surfaces. Vibrating a mass absorbs more of the sound energy.
Decoupling is achieved by using viscoelastic dampers between surfaces, and air gaps to prevent direct conduction. Air gaps need especial attention because they can resonate, especially at the lower frequency (1000-400 Hz) wavelengths of 13.5 to 33.76 in (34.3-85.75 cm). Resonance will transfer energy across the gap.
These techniques are applied in the following hypothetical example where a saloon is located above an engine room, and cabins are adjacent to engine-room bulkheads.
In a saloon above the engine room, sound can be attenuated in the design of the sole and the engine-room ceiling below that. For acoustic isolation in the sole build up a layered floor consisting of (starting at the bottom) a sub-sole, viscoelastic glue as a damper, an underlayment of acoustic mat made of dense rubber (similar to the mat used in horse stalls), then cement board and flooring.
In the engine room design the ceiling to provide attachment points for a drop ceiling. Apply composite insulation such as lead-fibreglass with the fibreglass rated at, say, R13. Since we are dealing with wavelengths of, say, 5- to 14-in, the thickness of the insulation should be in the same range. Install a decoupled drop ceiling consisting of two layers of non-combustible panels bound with viscoelastic glue. Several marine-approved panel materials are available.
Use spring ceiling hangers or other means to attach the panels to the attachment points in a decoupled way. In a capsize the spring hangers should be able to withstand high accelerations of mass to avoid detaching the ceiling. There should be an air gap between the insulation and the panels. Where the drop ceiling meets the walls, prevent flanking noise leaking through using a flexible acoustic sealer.
A ceiling of this type, combining mass, decoupling, resilient mounts and insulation is capable of attenuating noise 60-75 dB over 1000-5000 Hz [36].
Similar techniques could be used on the bulkheads where feasible. Consider alternate arrangements to simplify construction. For example, in the engine room use a viscoelastic glue to stick a non-combustible panel on the bulkhead, then attach the composite insulation. In the living space on the other side attach furring strips using neoprene rubber. If more isolation is needed incorporate rubber mat or more insulation. Always leave an air gap to prevent conduction.
If there is ductwork originating in the engine room, use round lined ductwork (insulated on the inside). Round ducts transfer less sound than square ones. In the engine room coat the exterior of the duct with a viscoelastic material, and cover it with a soffit to prevent exposure to direct sound. Consider a 90 or 180 degree bend to force sound to interact with the duct liner. Where possible, use serpentine lengths of lined flex duct to create a more complex path for sound.
Design an engine room entrance that has a double door. The inside door should be the watertight one (with a view port), and the outside one should be air tight. The space in-between would make a good place to hang ear protectors, etc. Both doors should have significant solid mass.
Finally, some cautions. Some complex isolation schemes were described above, but you should keep the design as simple and robust as possible. For example:
- The performance of two mass panels isolated by a viscoelastic glue can exceed that of a limp mass, such as lead-loaded composite insulation. It may be feasible to use just ~R13 fibreglass with the mass panels.
- A triple mass-panel sandwich alone that consists of a mass panel glued (viscoelastic) to either side of a bulkhead can achieve attenuations of 60 dB [36].
- Test (sound meters with a range of 35-130 dB can be rented.):
- Start with a basic installation of isolation in the engine room. Run the engine and use a sound meter to measure the noise in adjacent cabin areas. Upgrade the isolation to reach your sound goal.
- Or, build a small test box with a logging sound meter inside. Add test isolation externally. Evaluate the performance of your choices by suspending the test box in the engine room and running the engine.
Hull Openings & Closures
All exterior doors, hatches, vents, ports and windows should be watertight (not weather tight), located on the centreline, lockable and fitted with alarms. ISO 112216 gives specifications for boats under 24 m. Category A, for boats built for offshore, is designed for Force 8 winds and significant wave heights of 4 m (just over 13 ft) or more but excluding hurricanes, etc. Category B is also designed for Force 8 winds but significant wave heights only up to 4 m. Category C closures are for boats used inshore. Watertight means no water will pass through in either direction if the water has a head. A head is a column of water.
Inset portlights and windows look better and, incidentally, ensure conformance to standards. Deckhouse windows should not be submerged with the boat heeled 60 degrees. Any openings that could be submerged at 90 degrees heel should also be watertight. In particular, don’t compromise on the cockpit doors. There are some very nice patio doors that are only weather tight. These will not serve you well when following waves are breaking over the cockpit, in the event you are facing waves the wrong way around. Make sure all deckhouse openings are watertight.
Deck hatches and door sills should be at least 12-in off the deck. Portholes should be at least 20-in above the load waterline. Water and fuel intakes should be at least 4-in off the deck to prevent ingress of dirt. Openings for the engine room ventilation should be at least 36-in off the deck. (Air intakes on the side of the hull are susceptible to letting water in.) Extend the intakes down close to the engine room floor. In the event of capsizing, this will keep the inside opening above the waterline so that water doesn’t siphon in. The air intake should have a shutter to cut off air in case of an engine room fire. Fit all vents, dorades and other openings with metal rodent screens.

Fig 4-3 – Engine ventilation shaft extending to the sole of the engine room may prevent water intake in a capsize
Externally, sliding doors are safer and better than doors that latch back. Popular manufacturers of doors, hatches and port lights are Diamond/Sea Glaze [18], Freeman Marine [19] and Gebo [20].
The door from the pilothouse to salon, and interior companionways from the main deck to below deck should also be watertight and lockable. In Sharina’s case, I also want deadlights on the portlights and storm shutters on windows, the latter partly as a security measure. Storm shutters are designed to protect windows from flying objects in either a hurricane or a knock-down. Their main security use will be in rough ports, and when everyone is away from the trawler. Piracy is on the increase, and global warming will cause other troubles. Of course, deadlights and shutters are of no use if they’re open when you need them closed.
For knock-down protection, mild steel is the best choice. In a knock-down, all kinds of things will be breaking lose and smashing against the windows. Keeping the windows intact is essential if there is to be any hope of the trawler recovering.
For simple hurricane protection when moored, suitable materials are plywood, Plexiglas, aluminium and steel, depending on your requirement. Major factors are cost, and ease of installation. Effective shutters can be made from 3/4-in Mahogany plywood that is varnished. If the windows are inset, it is better to inset plywood shutters, fixing them in place with 4-inch barrel bolts every two feet. Insetting them will prevent the wind from tearing them off.

Windows with overhangs reduce significantly the amount of air-conditioning needed; curtains and blinds are less effective. A farmhouse I once designed had a veranda roof angled to match sun angles in different seasons so that windows were shaded in summer, for minimum heat gain, but exposed in winter, for maximum heat gain.
Any glazing materials should be (in order of descending strength) chemically reinforced glass (CG), tempered glass (TG), poly(methyl)methacrylate (PMMA), or polycarbonate (PC). Laminated glass is also available but may discolour over time. Glass should be thick enough, say 19 mm, to withstand water pressure in a capsize.
It’s unlikely that you will find theses types of glass with low-E. Low-E glass has a coating that reflects long-wave radiant energy. This helps keep in the heat in winter.
Thermochromic glass will also be available soon. It has a thin film made out of a material called vanadium dioxide. On cold days the film allows all sunlight in. On hot days, at a temperature of 25 C, the film blocks short-wave infrared rays, which are responsible for generating heat.
Super-hydrophilic coatings are also available to control condensation; but so far their life span is only one year.
Portlights should be inset for two reasons: they are architecturally cool, and they ensure conformance to ISO 112216 no matter what slope the sides of the hull.
Other hull openings are required for water intakes and outlets, propeller, thrusters and stabilizers, and instruments such as depth sounder, sonar, and logs, etc.
A sea chest is an interesting concept. This is a hull opening, say 15-inches square, which centralises water connections. (A sea chest is also a sailor’s footlocker.) The opening has a rectangular chest built up inside the hull to above the water line. It is fitted with a removable top to allow inspecting and clearing the external connections inside the chest. Its purpose is to supply a single-source for all of the intake water for engines, air conditioners, raw-water wash down, etc. Usually when a boat needs another source for water, you cut yet another hole in the bottom, with inherent issues including fouling, brass fittings, barnacles, etc. With the sea chest, these issues are localized.
There isn’t much information available about sea chests. Only DefeverR seems to use them. Advocates claim that, as a side benefit, so much water is forced through the sea chest opening that barnacles have to work a lot harder to attach. It’s unclear what effect turbulence inside the chest has on water circulation to the boat’s systems. It would seem reasonable to separate intakes and outlets as much as possible inside the box, or in separate chests. Exhaust headers and intake manifolds on racing engines might offer some design clues. I don’t think Sharina will have a sea chest.
The other main opening is for the propeller shaft. Traditionally, ships have used a stuffing box to seal the opening around the shaft. This is literally a box stuffed with marine grease. Stuffing boxes always leak a bit into the bilge. They’re fitted with a grease nipple and, every so often, you stuff them up.
More modern approaches exist in the form of seals. They tend to wear more on the shaft. A few can be replaced without removing the shaft. Sharina will have a stuffing box.
Keel Coolers
In most trawlers, the main hull openings for water are for open-system engine cooling and air-conditioner chiller, and a water maker. In an open system, seawater is circulated inside the boat to its machinery.

Fig 4-6 – A keel cooler uses the ocean water as a heat sink
– Photo with permission © Walter Machine company, Inc
– Photo with permission © Walter Machine company, Inc
There are three types of closed system. In the first, a heat exchanger located in the engine room separates the internal water system from the external seawater. In the second, the internal water system is routed through a keel cooler. Finally, an internal heat exchanger can be combined with an external keel cooler.
Keel coolers are like small radiators attached to the hull. Usually they are made from copper-nickel alloys. They should be flush mounted, to protect them. Stud types are easier to install than threaded types. Some builders put keel coolers in a sea chest.
Keel coolers must be connected to the boat’s Common Grounding Point. If not, they should have sacrificial zinc attached.
Channel-type coolers consist of a pipe cut in half and welded the length of the keel in a loop. Additives in the water control corrosion inside the pipe. If there is corrosion inside, the pipe will be thick enough to outlast the hull. Sharina will have channel-type keel coolers with an internal heat exchanger.
Exterior
The exterior of a steel hull is painted with a primer and topcoat. These are referred to as paint systems when used together as a complete system, providing chemically cured finishes resistant to abrasion, chalking, corrosion and chemical attack.
The primer is an epoxy primer. The topcoat, applied above the waterline only, is a high solids polyester urethane. The topcoat is applied to a high gloss finish.
The deck covering is largely a matter of individual taste. Traditionally, decks are wood covered, usually in teak. But wood is high maintenance. I personally prefer a low-maintenance non-skid coating such as Awlgrip® [21], GripTex [22], Tek-Dek [23] or Treadmaster [24]. Any wood decks, trim or interior panels should be finished with several coats of epoxy sealer and several more coats of a marine varnish that has UV inhibitors. The epoxy will keep the varnish from cracking and peeling, as wood swells and shrinks with moisture, and the varnish will keep the epoxy safe from UV damage.
Non-skid coverings, applied by spraying, rolling, or troweling, are really ‘low slip’. Nothing can prevent you 100% from skidding. Non-skid coverings are topcoats with an abrasive material added to the base paint. Additives range from polymeric compounds, walnut shells, and grit (very fine sand) to others. (A polymer is a natural or synthetic compound having a high molecular weight. It consists of millions of repeated linked units, made of simple molecules.)
Non-skid coverings are patterned. They are not applied to the whole deck. Areas around cleats and ventilators are masked off during application.
A wooden teak deck grating will make your boat somewhat cooler and more comfortable in the summer. I once had a 1968 long-wheelbase Land Rover – the 10-passenger Safari model with a 6-cylinder engine and a huge roof rack. This model was double-roofed – a so-called pavilion roof. It had the standard metal cabin roof. Attached to this were stand-offs, and attached to the stand-offs was a second metal roof, open at all the edges so air could flow between the two. In other words, it was a little bit like a tent fly, or the attic in a house. This kept the interior remarkably comfortable even on the hottest days. On the down side, such a deck grating will ice up or trap snow in bad weather. And teak doesn’t reflect radiant energy very well.
For these reasons, I am torn about what to do for the decks. Perhaps the answer is a synthetic imitation teak decking like Plasteak [25]. This doesn’t require maintenance like teak. Another possibility is to install radiant barrier insulation (RBI) in the cabin top (see Interior below) [26]. This would not trap snow or ice, but might be ineffective without a vented air space. A minimum space of 3/4-in is recommended between the barrier and insulation in residential applications. No marine data is available.
Another, simpler, solution is to mount an awning over the foredeck and the boat deck.
Interior
All interior hull surfaces are painted with an epoxy and urethane paint system to protect the steel from corrosion.
In living spaces, above the waterline, the hull should be insulated with closed-cell fire-retardant polyurethane foam or rubber foam like Armaflex [27]. The primary purpose of this is to control condensation. Secondarily, it reduces heating and air-conditioning losses through conduction.
Heat is transferred by conduction (contact), convection (air circulation within an enclosed space) and radiation (infrared absorption). There is so much emphasis by governments and builders on insulation, which reduces conduction, that it is not well understood that most heat transfer is by radiation. Up to 90% of downward heat flow on the cabin top is by radiant energy.
Urethane foams are plastics having gas-filled bubbles. This makes them light weight and a good insulator.
Closed-cell foam has varying degrees of hardness and insulation value, depending on its density. It can be used for insulation or flotation devices. A normal, closed-cell insulation or flotation urethane is between 2 and 3 pounds per cubic foot. It is strong enough to walk on without major distortion [28]. Polyurethane foam has an insulating value of R-5.6 to R-8.0 per inch [29, 30]. Open-cell foam is soft, and has a poor insulating value. It can outgas. It absorbs water, and is not suited to marine applications [28, 31].
Urethane foam degrades in ultraviolet light. Exposed surfaces should be coated with a special protective coating.
Installing radiant barrier insulation, also called low-emittance or low-e, in the ceilings may yield significant benefits in hot climates by reducing air-conditioning costs. RBI is a composite made of two layers of commercially fine aluminium (99.4% pure), bonded to both sides of a polypropylene insert. The polypropylene prevents the two aluminium foil surfaces from conducting heat. The surfaces reflect radiant energy. One of the first uses of this concept was in vacuum flasks, to keep liquids hot. The silvered surface inside reflects the radiant energy. The vacuum prevents convection. You’ve probably also seen the space-age emergency blankets in your local automotive or camping supply store.
On a fibreglass hull, the RBI can be bonded directly to the fibreglass. An air space between the RBI and the regular insulation is required for maximum efficiency. Fitting it to a steel hull is tricky. You would have to use one-sided RBI, to prevent galvanic action between the steel and the aluminium foil. Any screw penetrating the foil would cause galvanic action. It’s possible that any galvanic action would be self-limiting as the foil is sacrificed around a contact point such as a screw. In any event, the foil is very thin. White deck paint is almost as effective as RBI, and RBI has little value in cold climates [32], according to the literature.
Inside the hull, bulkheads and other interior fittings are usually screwed to hull stringers. This breaks the paint seal on steel hulls, and can lead to corrosion. Another way of doing this is to attach a neoprene rubber strip to the stringer, using waterproof contact cement. A plywood-furring strip is cemented to the rubber strip. Bulkheads, etc., are then screwed to the furring strip. This preserves the protective coating of the paint system, and flexibly mounts the interior.
Cabin walls are usually marine plywood with a veneer finish, which doesn’t reduce noise transmission much. Unless you want to listen to every noise from your neighbour or the adjacent head, make the cabin walls hollow, and insulate them with DFM mineral wool or an aerogel sheet [33] or use structural insulated panels (SIP). Aerogel is also an excellent thermal insulator, with a value of around R22 per inch.
Cabin soles are marine plywood or SIP, covered with a hardwood or tile.
A SIP consists of a solid foam core 4 to 8 inches thick (10.2 to 20.3 cm) with structural sheathing glued to the foam core. SIPs are advantageous when you want an insulated floor. They have a high strength-to-weight ratio and a high R-value. SIPs are also called foam-core panels, sandwich panels, stress-skin panels and structural foam panels.
Cores are made of expanded polystyrene (EPS), polyurethane (PUR) or polyisocyanurate (PIR), a special formulation of polyurethane. PUR/PIR is water resistant, not water proof, so it will absorb some water (typically 5%) and encourage mildew. The most common types of sheathing materials are oriented strand board (OSB) and plywood. Of course, marine-grade plywood is necessary in a trawler.
Both polyurethane and polyisocyanurate outgas HCFC. New, they have an R-value of around 9 per inch but ageing reduces it to 6-7. EPS is R-4. The R-value of EPS remains fairly constant over time, and it is less expensive per inch of foam. Polyurethane/isocyanurate panels, although almost twice as expensive, are more fire and water vapour-diffusion resistant than EPS. Panels made of PUR/PIR are typically 3.5 inches (89 mm) thick.
Because PUR/PIR does not bond easily, quality fabrication is especially important to ensure a long life and performance. The panels must be glued, pressed, and cured properly to ensure that they do not delaminate. Tough choice, isn’t it?
Tile flooring is not recommended in a small fibreglass hull, due to the twisting and flexing. I think it can work in a 50-ft or larger steel trawler. While in a home tile can be bedded in a mortar over plywood, plywood contracts and expands too much in a boat to provide a firm footing. This, plus vibration, can easily crack mortar and tiles. In a boat, cover the plywood (min 3/4-in) or SIP sole with a rubber membrane and then 1/2-in of impermeable cement board such as the original Wonderboard [34]. Leave 1/8-in between sheets and caulk between them. Attach the tile with a multi-duty acrylic-modified thinset. Consider means of isolating tiled sections from each other with wooden expansion strips, and from steel stringers with neoprene.
Summary
The best hull material for a serious offshore passagemaker is steel because of strength and ease of repair; although a glass-reinforced-plastic NIDA-sandwich is also very strong. A swim platform at the stern doubles as a boarding platform – a safety feature required in many jurisdictions – and mount for a stern thruster. Ideally there are three or more watertight bulkheads.
All exterior doors, hatches, ports and windows are watertight for storm protection. They should be lockable and fitted with alarms for additional security in a chaotic world. Heat exchangers such as keel coolers do not bring seawater into the boat. The exterior hull is finished with a complete paint system, incorporating a non-skid topcoat. The interior hull is finished with an epoxy and urethane paint system. In living spaces, three inches of closed-cell polyurethane foam yields an insulating value of R-18.5. White deck paint, teak gratings or radiant barrier insulation in the ceilings significantly reduces air conditioning needs. Insulating cabin walls with mineral wool or aero gel provides privacy.
References
1. Hartley & Brookes Associates, http://www.ferroboats.com/
2. The Ferro Cement Network, http://www.ferrocement.net/
3. dk yachts, http://www.dkyachts.com/
3-1. NIDA Core, http://www.nida-core.com/
4. Kady-Krogen Yachts, http://www.kadeykrogen.com/
5. The causes of Boat Hull Blisters, Thomas J. Rockett, Ph.D. and Vincent Rose, Ph.D., Department of Chemical Engineering; University of Rhode Island; Kingston, Rhode Island, U. S. Coast Guard Grant #1501.83, http://www.daviscoltd.com/nams/Documents/Blister_Report.html
6. Fiberglass World, http://www.fiberglass.com/
7. Pacific Northwest Pollution Prevention Resource Center, http://www.pprc.org/
8. Alacan Airex, http://www.alcanairex.com/products/e/100/110p01_e.htm
9. Diab Inc., http://www.diabgroup.com/
10. See 3-1.
11. Foam Core Materials in the Marine Industry, Trevor Gundberg, Composite Materials Engineer, DIAB Inc., BoatDesign, http://www.boatdesign.net/articles/foam-core/
12. Fibresource, http://www.fibersource.com/f-tutor/aramid.htm
13. E. I. du Pont de Nemours and Company, http://www.dupont.com/kevlar/
14. DPS Composites, http://www.dpscomposites.com/
15. The Complete Guide to Metal Boats, Bruce Roberts-Goodson, International Marine, McGraw-Hill Corporation, ISBN 0-07-136444-7
16. Cape Horn Yachts, http://capehornyachts.com/
17. vero marine, http://www.veromarine.co.nz/dirvz/marine/marine.nsf/Content/Home
18. Diamond/Sea Glaze, http://www.diamondseaglaze.com/
19. Freeman Marine Equipment, Inc, http://www.freemanmarine.com/
20. Gebo Marine Glazing, http://www.boomsma.com/
21. Akzo Nobel, http://www.awlgrip.com/
22. Dash Multi-Corp, http://www.dashmulticorp.com/textiles/texnspgtex.asp
23. Tek-Dek, http://www.tek-dek.co.uk/
24. Plastimo, http://www.plastimousa.com/treadmaster.htm
25. PlasTEAK, http://www.plasteak.com/
26. Reflective Insulation Manufacturers Association, http://www.rima.net/
27. Armacell Engineered Foams, http://www.armaflex.com/
28. Building Envelope Solutions, Inc., http://www.foam-tech.com/
29. Alliance for the Polyurethanes Industry, http://www.polyurethane.org/
30. Polyisocyanurate Insulation Manufacturers Association, http://www.pima.org/
31. Spray Polyurethane Foam Alliance, http://www.sprayfoam.org/
32. Radiant Barriers, Consumer Energy Information: EREC Reference Briefs, Office of Energy Efficiency and Renewable Energy, http://www.eere.energy.gov/consumerinfo/refbriefs/bc7.html
33 Aspen Aerogel Inc., http://www.aerogel.com/
34. Custom Building Products, http://www.custombuildingproducts.com/
35. Double hull, http://en.wikipedia.org/wiki/Double_hull
36. The Green Glue Company, http://www.greengluecompany.com
37. New boat aims to make SEALs' travels less painful, CNN, http://www.cnn.com/2008/TECH/01/13/seals.new.boat.ap/index.html
© 2008 David Shaw
david.shaw.x23@gmail.com
5 comments:
Steel building construction has 48% of the total market share of construction. It includes commercial buildings, industrial buildings, temporary shelters, storage units, churches and air hangers
Thanks for this post, I like the fig 4-2, its really looking fantastic. In this post its clearly defined about hull construction. Very informative and useful.
Wow, this is a great and informative article.
I agree that foam core sandwich panels are certainly gaining in use and popularity for marine construction. I was surprised to see you mention balsa wood as a substitute for foam. I would think this would get wet and rot?
I'd like to commend you on a very through blog. As a mechanical engineer and a student of boats I appreciate the thoroughness. However, I think it is an oversight not include Aluminum. Even though Aluminum costs more per pound, because of the lower density you use fewer pounds and it is easier to work than steel (you can cut it with wood saws), which helps offsets the higher material cost. For small boats, where you experience minimum gauge issues with steel, aluminum can produce a significantly lower weight design. The marine grades have superior corrosion protection to steel, which is why aluminum boats have superior resale value. You do need to be very careful of dissimilar materials corrosion and induced current electrolysis. Like steel, aluminum is easier to repair than FRP, although it is harder to weld than steel so it could be harder to find competent welders in third world countries.
Создание сайта будь то сайт – визитка, корпоративный сайт, [url=https://webprospekt24.ru/prodvizhenie-sajtov-prokopevsk]продвижение услуг[/url], интернет магазин или мощный портал проходит в несколько этапов.
Уникальный контент - залог успеха продвижениея
Post a Comment